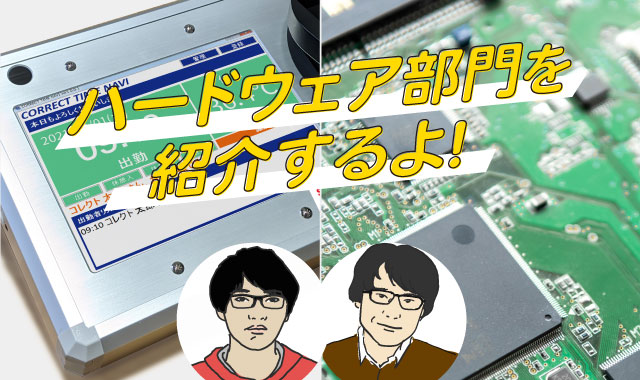
当社、ユニテックシステムの社名の由来はご存知ですか?ユニテックシステムは「Union Technology System」の「Union = 融合」、つまり、ソフトウェアとハードウェアの「融合」という意味が込められています。ソフトウェアの事業領域である、人材派遣管理システム「スタッフナビゲーター/キャスティングナビ」がシェア率No.1を獲得するなど、近年、ソフトウェア事業で露出の多い当社ですが、創業当時からの礎となっているのがハードウェア事業です。
ユニテックシステムは、昭和61年 千代田区岩本町にて創業し、その4年後にはハードウェア部門が発足。その後は、データチャネルデコード基板/デジタル音声基板/オーブンコントローラボードなどを受託開発し、多くの企業に納入して参りました。ユニテックシステムの黎明期を支えたのは、他でもないハードウェア事業部門であり、その“ものづくりのDNA”は35年後の今も社内に引き継がれています。
目次
ハードウェア部門で作っているもの
ハードウェア部門では、大きく分けて「自社開発製品」「受託開発製品」の2つを開発しています。まずは、「自社開発製品」である“コレクトタイムナビ”の製作現場をご紹介します。
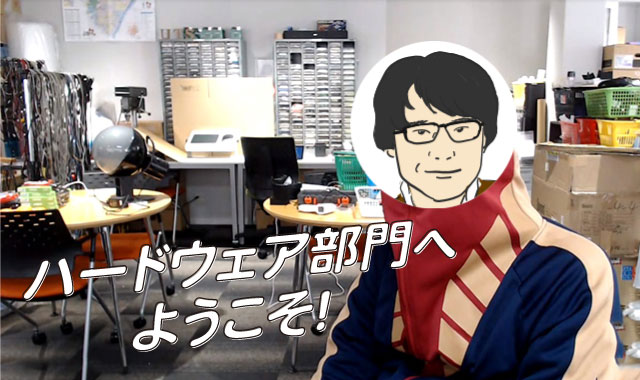
【自社開発】手のひら静脈認証式 勤怠管理システム「コレクトタイムナビ」
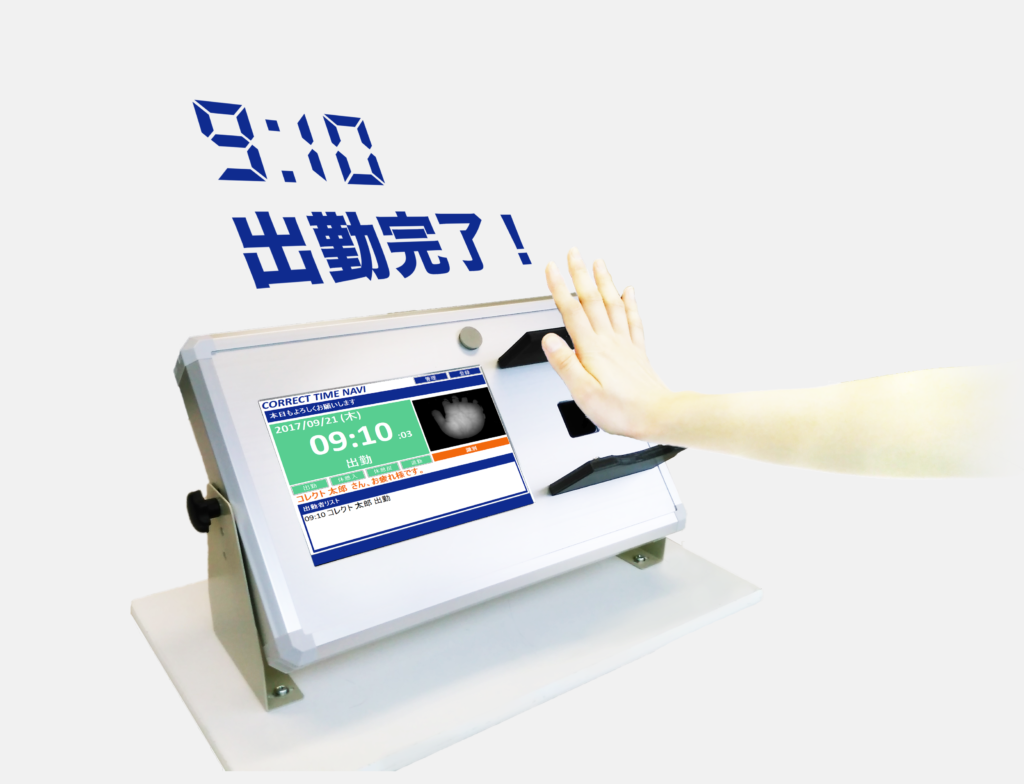
コレクトタイムナビは、手のひらをかざすだけで簡単に出勤・退勤時刻を記録できる勤怠管理システムです。2016年の発売開始より、製造・物流業界を中心に累計約10,000人の従業員が利用しており、その筐体は当社のハードウェア部門が設計・開発しています。
▽製品紹介Webサイト 手のひら静脈認証式 勤怠管理システム「コレクトタイムナビ」
https://www.uts-navi.com/ct-navi/
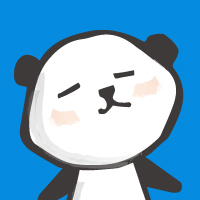
こんにちは。
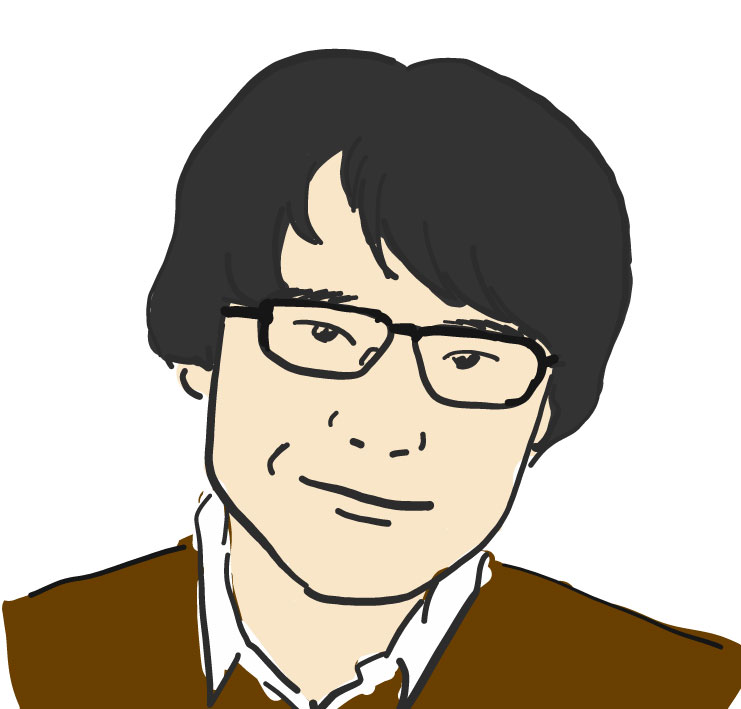
今日は、コレクトタイムナビができるまでのお話を紹介しますね。
ウチガー:
当社はミャンマーにオフショア開発拠点があります。当時、ミャンマーでは勤怠の不正打刻が横行していたようで、「どうにかできないか?」と当社のミャンマー拠点に相談がありました。当社の担当者が詳しく話を伺うと、工場へ出勤した際に、友人のICカードも打刻して友人も出勤したことにしてしまう、といった不正打刻が多く見受けられていたようです。
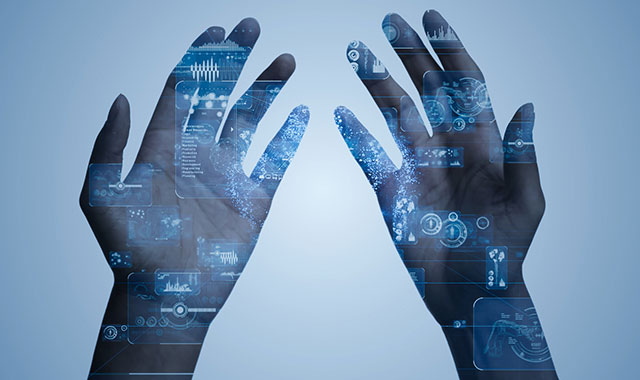
当初は、ノートパソコンに手のひら静脈認証機を接続してミャンマーの現地企業に運用いただいてましたが、ノートパソコンを置きっぱなしにしておくと現地では、盗まれてしまう恐れがあるとのこと。そこで、パソコンと手のひら静脈認証機が一体化したものを開発することになりました。それが上記の写真でも登場したBOX型のコレクトタイムナビです。そのBOX型(筐体)を開発しているのが、私たちハードウェア部門です。
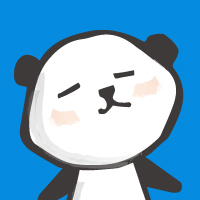
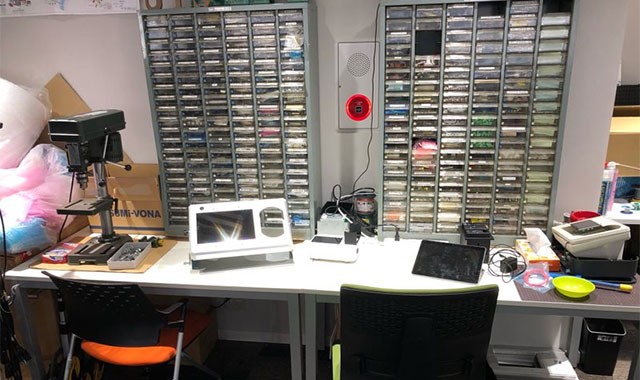
ウチガー:
開発の流れをざっくり説明しますね!
筐体を設計・組立てる
①BOX型の開発
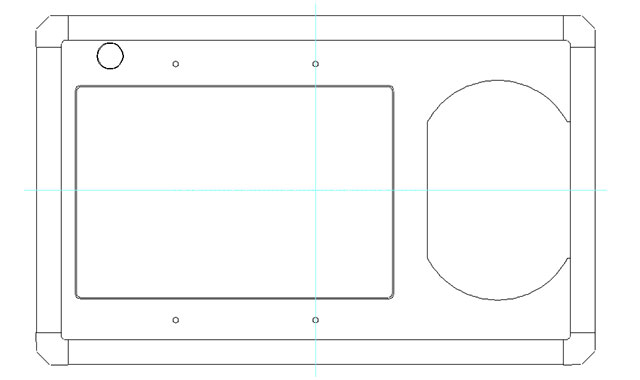
ウチガー:
ロット、数十~数百規模の量産ですので、専用ケースをイチから設計・開発するとコストがかかってしまいます。その為、市販の金属ケース・樹脂ケース(工業用に売られているもの)から適切なものを選定し、そこに追加工をしています。中に設置されるデバイスの形状を考慮し、最適な位置に穴あけや金具などの取りつけを行っていきます。
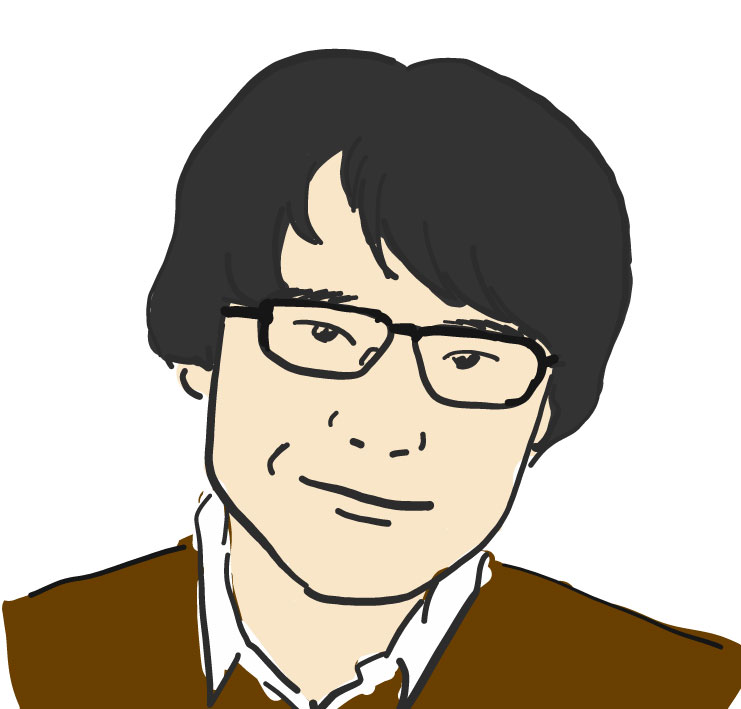
②組立てる
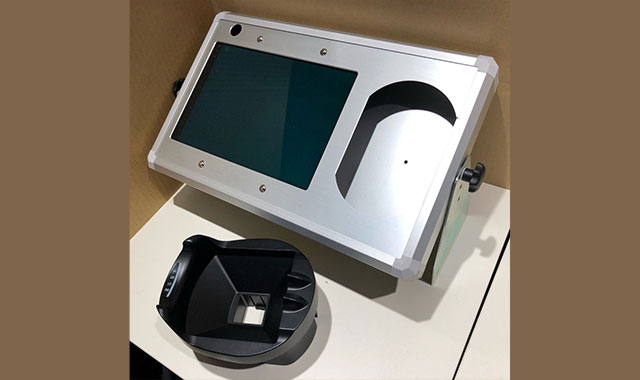
ウチガー:
試作品の筐体が工場から送られてきたら、設計書どおりにできているか確認する「受け入れ検査」を行い、問題がなければ組立工程へ進みます。実際に組み立ててみると、設計段階では気付かなかったことが多々発生しますので、そのまま量産に進んでしまわないように、この段階でしっかりチェックして対応しておきます。
筐体の中には、タブレットが設置されます。 配線の引き回しを考慮して、バランスよく部品配置を行います。
③動作確認をする
通電するか、センサーが反応するかなどの動作確認を行います。また、設置したときに安定感や、突っかかりがないかなどの筐体全体をチェックします。
④量産委託
製造委託先のやり方次第ですが、今回は委託先の作業者と打合せを行い、共に実地で組込し、製造・動作確認の手順を作り上げました。以後、それに従って量産、納品してもらいます。
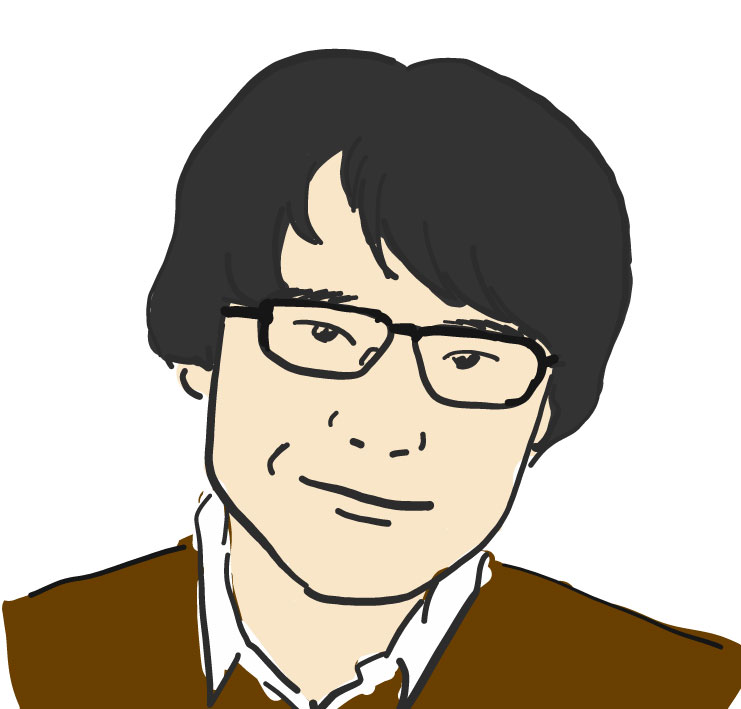
3Dプリンタを利用した部材開発
①3DCADソフトで造形物を設計する
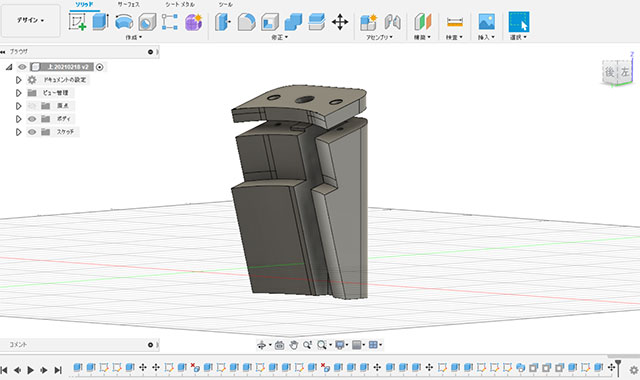
安齋:
3DCADとは、3次元空間上に3Dモデルを作成するソフトウェアです。3Dプリンタで造形物をプリントするには、設計図となる3Dデータが必要になり、3DCADソフトでモデリングします。
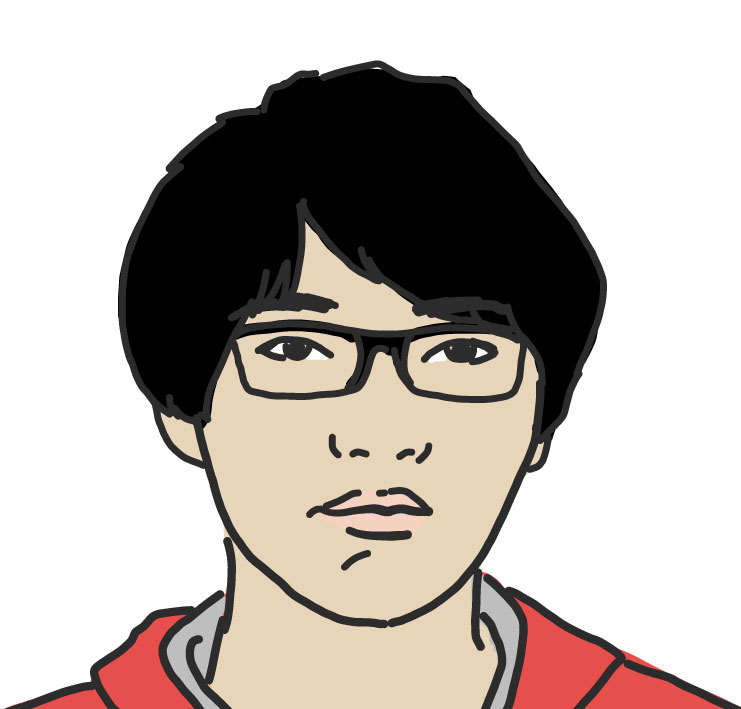
微調整しながら、何十回も試作しましたね。
②3Dプリンタによる印刷(造形)
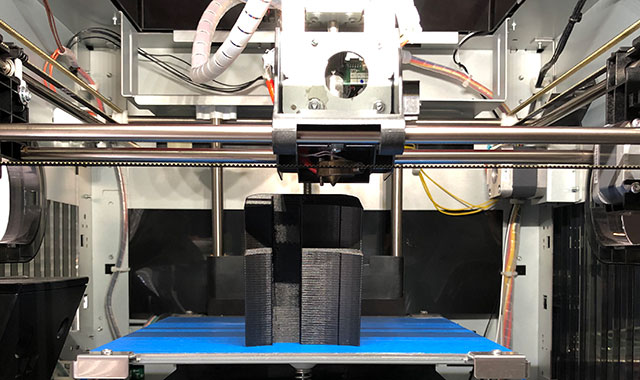
安齋:
3Dプリンタはデータを元に、樹脂や金属を一層一層少しずつ積層しながら、立体物を作りだしていきます。ユニテックシステムで所持している、熱溶解積層法3Dプリンタは熱でフィラメント(樹脂素材)を溶かして、それを自動で設計図通りに積み上げていく仕様です。今回は、手を置く部分に合わせてフィラメント(樹脂素材)の色をブラックにしました。
上の部分の印刷に1時間、下の部分の印刷に5~6時間がかかります。
③コレクトタイムナビへの取り付け
回路基板、3Dプリンタ造形物をコレクトタイムナビに取り付けて、動作確認をします。
④量産委託
同様の手順を経て同じ委託先で量産します。
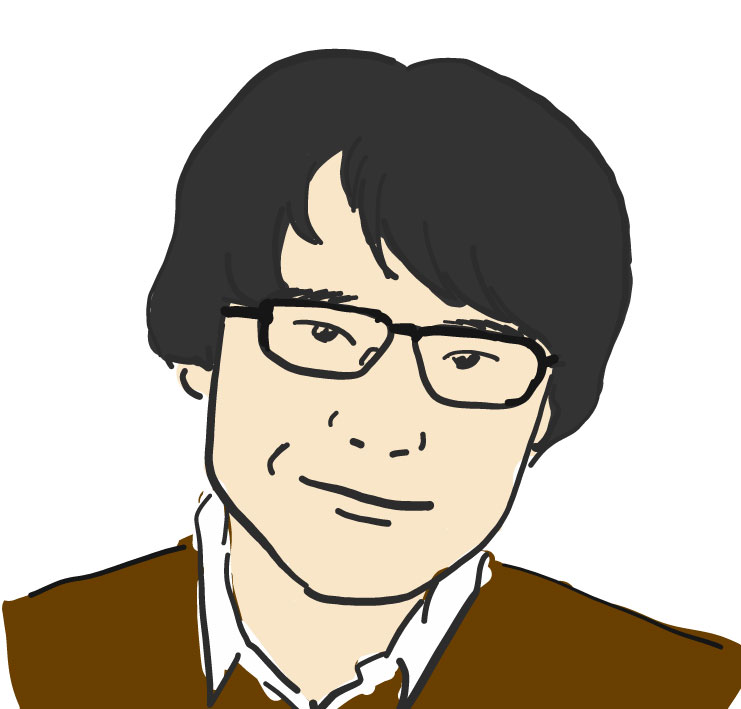
【受託開発】組込回路を中心とした業務用機器の設計開発
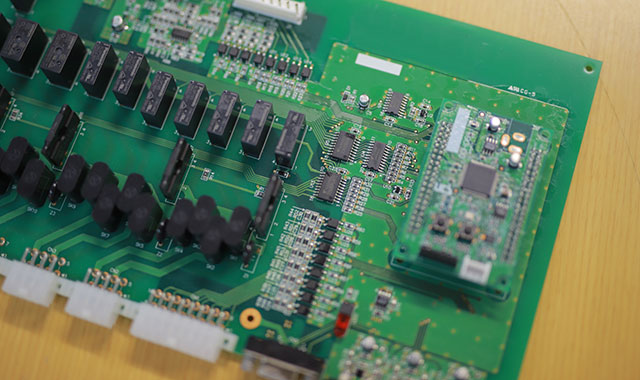
ウチガー:
電気製品には欠かせないのが基板。PC、冷蔵庫、テレビなどあらゆる電気製品に基板が使われています。みなさんも家電のカバーを外したときなどに、見たことがあるのではないでしょうか?基板は、絶縁体の板に導体の配線を配置させたもので、抵抗器やコンデンサ、半導体などの部品がそこに実装されています。基板は、それぞれの電子部品を電子回路的に適切に配置し、役割を与えてはじめて電子回路として動作するようになっています。
ハードウェア部門では、こういった基板設計の技術を使って受託開発を行っております。
◆設計~開発・量産まで一貫してフォロー
ファブレス(自社工場は保有していない)ではありますが 、 外部工場とタイアップすることで、 設計 開発 量産 (部材調達 ・実装・調整 ・検査) を一貫してフォローしています。モータ制御基板 ・ 温度制御基板を得意としています。
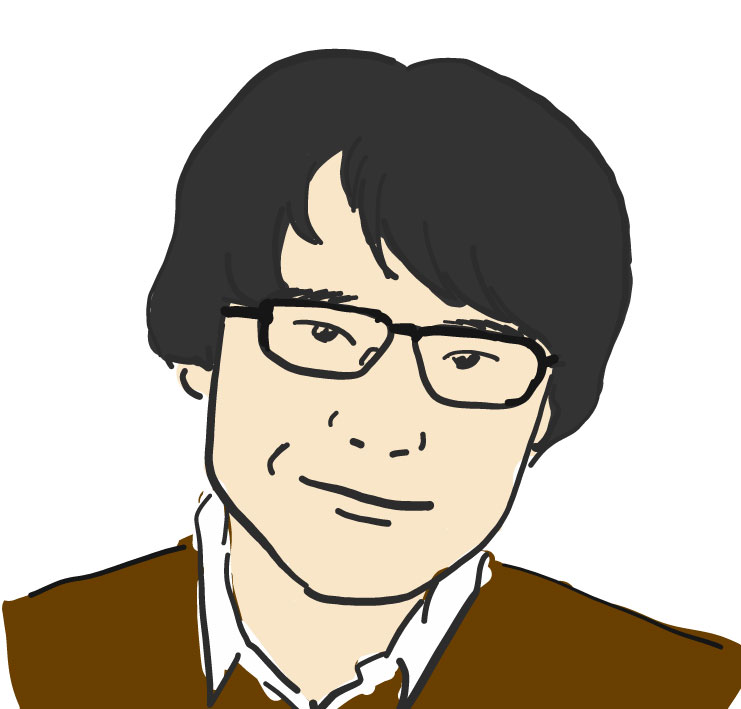
◆基板のリメイク
部品製造中止やメーカー廃業等が理由で、製造できなくなった基板を新しい部品で作り直しています。例えば、はんだ付けロボット等の産業機械や、漁船の冷凍機の制御基板などです。
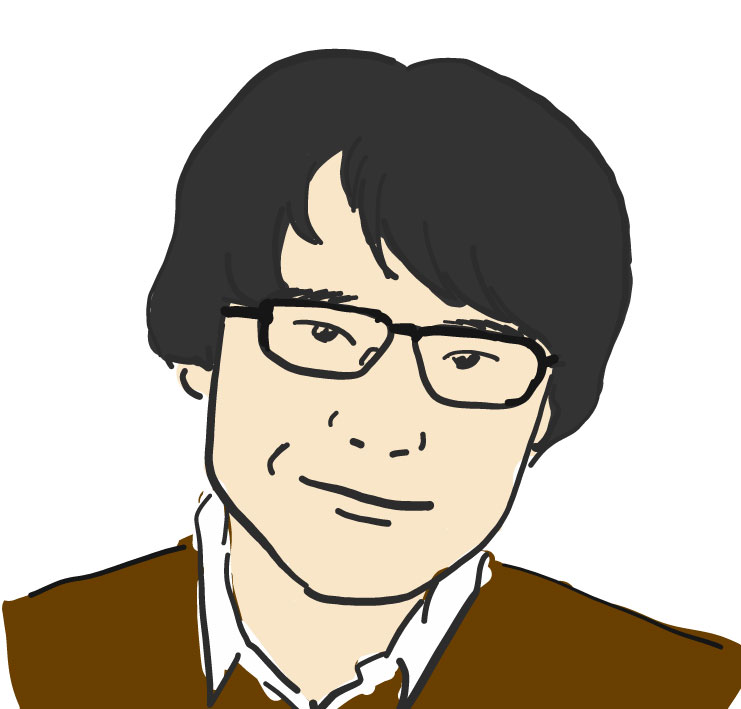
自分で回路設計して実装して、
動作した瞬間に、やりがいを感じられます!
まとめ
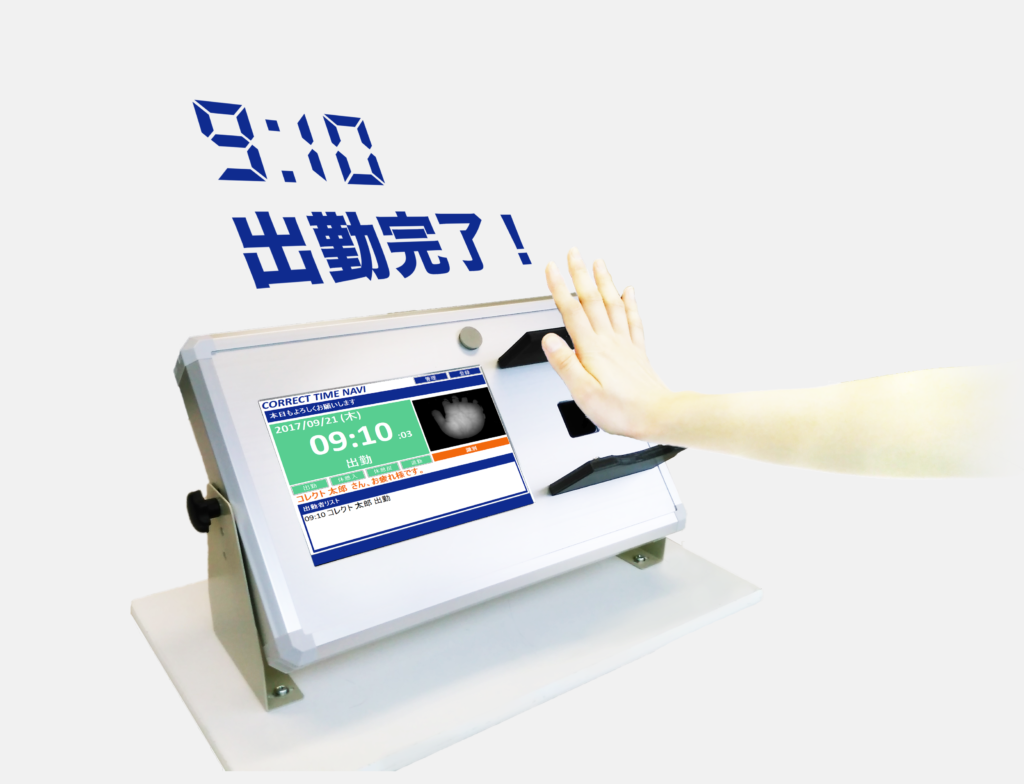
▽製品紹介Webサイト 手のひら静脈認証式 勤怠管理システム「コレクトタイムナビ」
https://www.uts-navi.com/ct-navi/
ウチガー&安齋:
ユニテックシステムが持つ、ハードウェアとソフトウェアの技術がまさに“融合”して、誕生したのが手のひら静脈認証式勤怠管理システムシステム「コレクトタイムナビ」です。両部門が社内に存在しているからこそできる実行力やスピードの早さというものは、ユニテックシステムの大きな強みです。今後も両方の技術を高め合い、ユニテックシステムだからこそ提案できる製品をたくさん生み出していこうと思います。最後までお読みいただきありがとうございました。